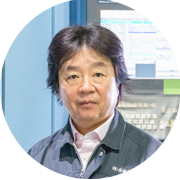
井部 良則さん
株式会社井部製作所 代表取締役
1983年、高校卒業後、株式会社井部製作所に入社。福井県にある工作機械メーカー株式会社松浦機械製作所に出向し3年間技術を学ぶ。2005年、創業者である父の急死を機に代表取締役に就任。社是やマネジメントシステムなどを導入し、事業を拡大。後進への技術伝承として独自の教育プログラムを導入。趣味はゴルフ。
東日本大震災と原発事故という未曽有の災害から10年。浜通り地域の復興のために何かできないかと、地元だけでなく、福島県外の企業も協力を惜しまない。千葉県山武市で精密機械部品の機械加工、プレス加工をする株式会社井部製作所もその1つ。2017年に南相馬市に工場を開設し、地元で採用した社員たちが、生き生きと仕事に取り組んでいる。代表取締役である井部良則さんを訪ね、福島へ進出した思いをうかがった。
「被災地の力になりたい」を原動力に
半導体製造部品などを作る工場を新設
2016年に設立50周年を迎えた井部製作所は、プレス金型やプレス加工業として東京都目黒区に創業。当初はスーパーなどで使うレジスターの部品や、手形や小切手、領収書などに印字するチェックライターの部品を製造していた。転機が訪れたのは、1983年。取引先から精密部品加工の相談を受けた。
「これまで請け負ったことのない難しい仕事で、当時の日本の中小企業には数台しかなかったコンピューター数値制御によってさまざまな切削加工ができるマシニングセンタを導入。私も工作機械メーカーに出向し、3年間みっちり技術を学びました。仕事は無事に納品でき、これをきっかけに精密機械加工に注力していきました」と井部さん。
特殊な工作機械を持っていたことや、それを扱える同社の高い技術力が評判を呼び、半導体製造装置部品の製造を主軸に、航空宇宙、医療、エネルギーなど、取り扱う領域が拡大。2010年には、航空宇宙・防衛分野の標準規格である「JISQ9100」認証を取得した。
事業が拡大するたびに増改築を繰り返した千葉工場が手狭になり、工場の建て替えを検討していた。そんなタイミングで起こったのが、東日本大震災だった。
「被災地復興のために、力になりたかった」と、被災地への進出を決めた心境を語る。「福島には取引先もありましたし、福島イノベーション・コースト構想が掲げる医療機器や航空宇宙関連、ロボット産業は、まさに弊社が力を入れていきたい分野で、事業の拡大を見込めたのも魅力でした」
南相馬市職員の熱意と親身なサポートもあり、南相馬市にある工業団地に進出を決めた。「津波・原子力災害地域雇用創出企業立地補助金」を活用することで、土地や建屋、設備などの初期費用を大きく抑えることにも成功。また、浜通り地域は雪がほとんど降らず、常磐自動車道を使えば千葉工場まで4時間ほどで到着するなど、交通の便が良かったのも決め手の1つだった。
2年弱の準備期間を経て、およそ1,200㎡もある工場が完成。日本に数台しかない最新式のマシニングセンタやCNC旋盤などの大型機械が所狭しと並ぶ姿は圧巻だ。現在、17名の従業員が、半導体製造装置や航空機エンジン部品の製造を行っている。地元の専門学校を卒業した新卒者2名と、中途採用した10名を採用し、雇用創出にも貢献している。
日本の半導体技術を支える
1000分の1ミリにこだわる職人技
井部製作所の技術力の評価は高い。半導体を作るためにはシリコンの塊を薄く切る必要があり、最大で800ミリ、厚さ0.1ミリのステンレス製の円盤状の特殊なカッターを製造している。この半導体製造装置の部品は、日本で同社でしか加工することができない。
「ステンレスの板をプレスし円盤状に抜くのですが、いかに反りを出さないか職人の腕の見せどころです。特殊な金型を製作し、プレス機の加工条件を細かく設定するなど、40年以上培ったノウハウがなによりの財産です」
航空機のエンジン部品に使われるブレード(タービンの羽根)は、高温に耐えられるようチタンが使われている。チタンは難切削素材の1つで、粘りが強く固い特徴を持つため、取り扱いが難しく、発注元から製造マニュアルをもらうことも少なくない。しかし、指定された工具や治具を使い、同じ条件で作っても、必ずしも同じものができるとは限らない。だからこそ、図面を見て、工程を考え、完成したときの嬉しさはひとしおだと言う。
仕上がりを逆算し、オリジナルの治具を制作(写真左)。日本に数台しかない航空機部品の難削材加工をするMAKINO製5軸マシニング「T1」
コンピューター制御の最新式の工作機械があれば、誰でも、ボタン1つで簡単に作れてしまうのではないか。「そう簡単だったらいいですけどね」と井部さんが笑う。
まず、マシニングセンタをはじめとした最新の工作機械を使いこなすまでに、3年ほどかかる。さらに、求められる精度が、1000分の1ミリ単位と非常に高い。髪の毛の太さが約0.1ミリなので、それを100等分した大きさだ。部品によっては誤差を1000分の5以内に収める必要があるのだそう。
人間の手によって仕上がりの微妙な違いを修正。室温を一定に保った検査室に設けられた3次元測定機を使いクオリティを管理
「機械は進化していますが、やっぱり職人さんの手の感覚はすごいですよ。機械が削ったところを触るだけで、細かな凹凸が分かりますから」。各工程での検査と、3次元測定機を使った最終検査の2重チェックを経て納品。もし不備があったときは原因が分かるまで調査し、同じ失敗を繰り返さないよう従業員全員が参加する不適合対策会議で共有。不備率を年間0.5%以内に抑えるよう努めている。
突然訪れた、社長就任。
従業員とともに困難を乗り越える
改めて井部製作所の強みを尋ねると、「CAM/CADを使った5軸加工や、精密部品の特殊加工も強みですが、従業員あっての会社だと思っています」と答える。
井部さんが30代後半のとき、創業者である父が亡くなり、急きょ会社を継ぐことになった。機械の操作や営業に関しては、しっかりやっていたので問題はなかったが、会社経営、社員マネジメントには苦労したと当時を振り返る。
「お金のことは取引銀行などに教えてもらい、仕事の悩みやグチは母親や妻が相手になってくれました(笑)」。さらに、40歳を前にした若い社長を支えてくれたのは、これまで一緒に働いてきた従業員たちだった。先の「従業員あっての会社」という言葉には、高い技術力を持つ人材という意味だけでなく、井部製作所の大変な時期を一緒に乗り越えてきた仲間という意味も込められているのかもしれない。
人がすっぽりと入るほどの大型工作機械を駆使し、精密な部品を手がける
そんな井部さんの思いは社是である「和協」にも現れている。「会社全体の和を大事にし、お互いに協力できる会社をつくりたい」という思いが込められ、社員とともに議論しながら決めたそう。営業も職人も、検査担当者も、誰もが井部製作所の一員として仕事に誇りを持っている。
「半導体も航空宇宙メーカーの部品も、目に見える場所で使われるものではありません。航空機なら、自分たちが作った部品がエンジンとして組み立てられ、安全に空を飛んでいるのを見ると嬉しく思いますし、やりがいを感じます」と胸を張る。
福島イノベーション・コースト構想とともに
次代につながる主軸事業に挑む
南相馬に工場を開設し、もう4年が経とうとしている。人工知能(AI)産業の隆盛もあり、同社の6割ほどを占める半導体製造装置部品の需要は右肩上がりだという。ただ、事業の柱が1つだけでは需要の波の影響が大きく経営的に不安定なので、第2、第3の柱として「医療」「航空機」「ロボット」領域への事業展開を検討している。
「医療分野では、手術台や介護ベッドなどを手がけていますが、今後はインプラントや人工弁、内視鏡の先端など、人体に入るものをしたいですね。南相馬市がロボット産業に力を入れていますし、福島ロボットテストフィールドもすぐ近くにあるので、何かしら協力できたら、と考えています。また、職人として技術的な部分をもっと追求していきたい思いもあります。新しい素材も開発されますし、求められる部品の難易度も上がっていきますから」
会社の入口にマネジメントシステムの認定書が飾られ、同社の技術力の高さを教えてくれる
今後の労働力不足を見越し、工場内にロボットを導入し、無人化・自動化を検討している。今は、素材を積んだパレットを工作機械にセットし、金曜日の夜から週末にかけ自動で製造を行っているが、いずれは素材の取りつけ、仕上がった部品の取り外し、検査室への運搬といった工程をロボットで代替したいと話す。
南相馬工場の敷地の一部はまだ更地のままになっている。「いずれは、ここに第2工場を建てるのが夢なんです。息子である3代目が千葉で働いているので、何をするかは彼が決めてくれればいいと思います」と目を細める。
福島の復興に役立ちたいという思いから工場を新設し、地元の雇用創出と事業拡大を実現させた。福島での新たな出会いをきっかけに、さらなるステージに向けチャレンジする同社から、今後も目が離せない。
株式会社井部製作所
1966年、東京と目黒区でプレス金型、プレス加工業として、先代井部一郎が創業。1984年千葉工場開設。1985年マニシングセンタ、CNC旋盤部門を開設。2010年、航空宇宙・防衛分野の標準規格「JISQ9100」の認証取得。その後、医療、環境の認証も取得。2017年に南相馬工場開設し、半導体製造装置、航空宇宙防衛部品、エネルギー関連、医療機器の精密部品加工を手がける。
Hama Tech Channelとは
豊かな未来を切り拓くリーダーとテクノロジーにフォーカス。
「社会を良くする」力強い変革を応援する、福島発・未来共創型メディアです。
「福島イノベーション・コースト構想」の一環として、
地域の未来を切り拓く取り組みを発信しています。